Mould & Die Industry
Dies and Moulds are used in numerous manufacturing procedures and in several situations the process would require induction heating. The procedure of injection molding of plastic or rubber products needs pre-heating of the molds to a higher temperature, to confirm the proper flow or curing of the injection-molded material.
Induction Heaters are widely used in Mould & Die Industry for applications like Preheating of tools and molds for plastic injection molding, Die heating for catheter tipping and medical products manufacturing, Heating of molding tools for curing of rubber product and automobile tires, Preheating of casting molds in the metal casting industry, Die and platen heating for metal stamping and forming, Heat treating and hardening of stamping and punching tools and dies, etc. Precision Instruments & Allieds’ Induction Heaters Induction heating technology is very clean and energy-efficient which results in less energy lost to the surrounding air.
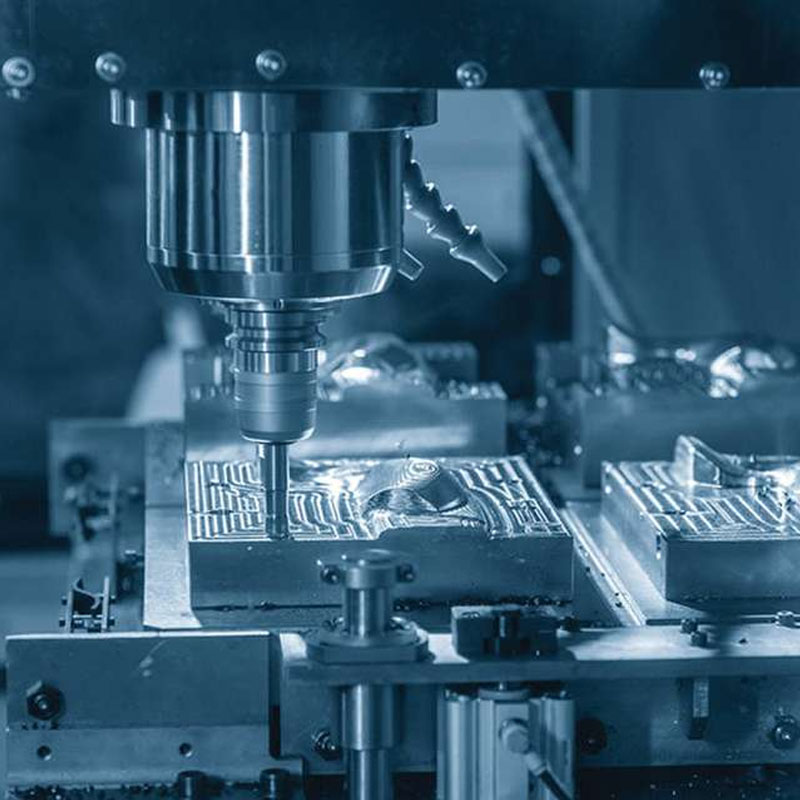
Induction Heaters by Ratings
The life of bearings and other torque transmitting steel components, which are shrunk-fit on shafts, may get cut short due to rough handling and faulty installation or mounting methods. This can be prevented by expanding them by induction heating for the purpose of mounting the component. …. Read More
The Precision Induction Heater (PIH: 2000) operates on a 3 phase, 230 V power supply and has a power capacity which ranges from 2KVA. Its light duty induction heater. It is fast, safe and economical heating of bearings is best features this with intelligent microcontroller based programmable electronic controls. …. Read More
Precision 20KVA Industrial Induction Heater is safe, fast and economical heavy duty Induction Heater which uses latest technology intelligent microcontroller based electronic controls. When alternating current flows through a coil wound around a component or part; it generates an oscillating magnetic field, which contains current in the component. …. Read More
The magnetic field takes the path of least resistance and also due to the skin effect; the outer periphery of the part gets heated more rapidly than the core. Based on the above principle, a ring shrunk fitted on the shaft will get heated more rapidly causing a temperature differential between the two. …. Read More
When a component is heated with the induction coil it acquires magnetism strong enough to attract iron particles, iron dust etc. To deal with this phenomenon, it is necessary to eliminate the residual magnetism after heating. The designs of the control panel of precision 80KVA…. Read More
Based on the above principle, a ring shrunk fitted on the shaft will get heated more rapidly causing a temperature differential between the two. The difference in the temperature will cause the ring to expand to a stage where it overcomes interference and can be dismounted easily…. Read More